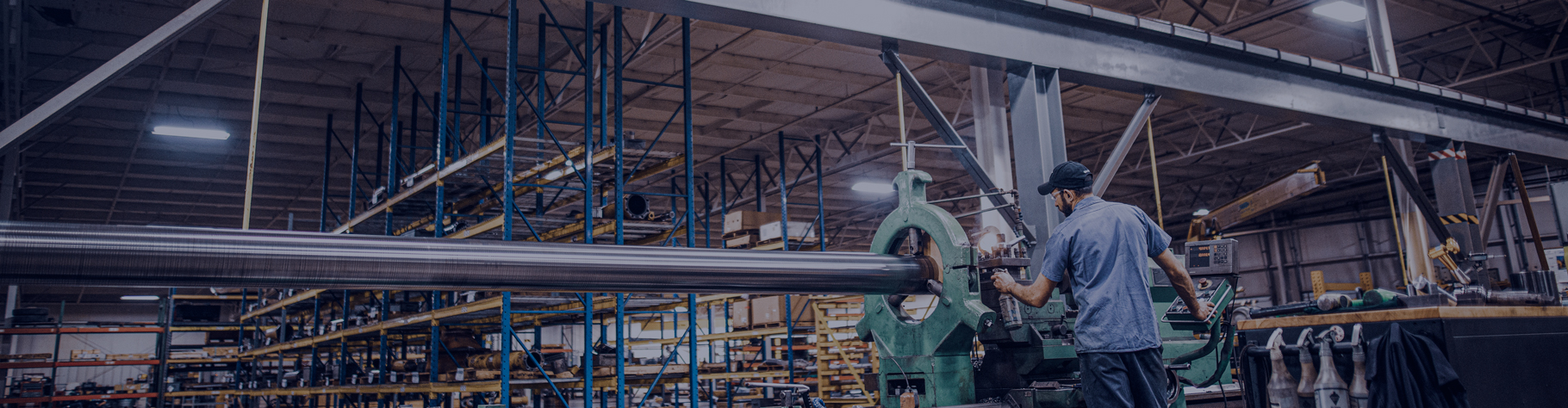
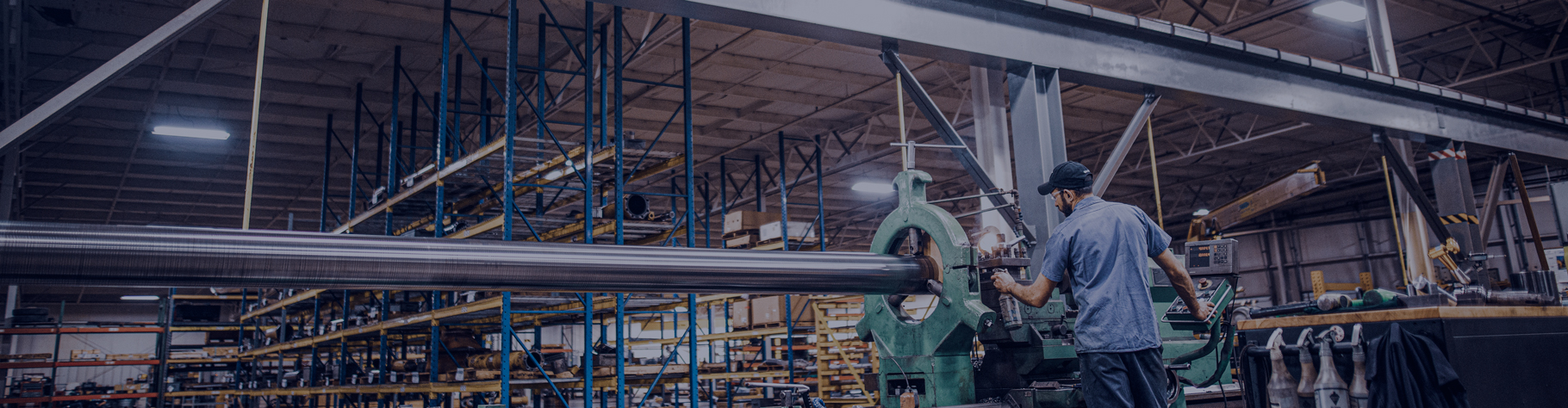
Honing is a metal finishing process akin to fine grinding, which is used to create the optimal surface finish in a hydraulic cylinder tube. Any respectable hydraulic shop should be providing honing service as a critical part of a cylinder rebuild. It is a simple process and a relatively small portion of the total cost of a cylinder repair.
A properly honed tube is the basis for a superb seal, smooth operation and extended seal life for any hydraulic cylinder. Leaks are the most widely cited repair indicators that will prompt a cylinder repair. When leaks are present, contaminants could enter the system. Contaminants can create scratches, low spots and other irregularities in the cylinder tube wall. These irregularities accelerate seal wear and eventually cause internal leaks. Internal leakage is a silent killer that decreases performance. Deglazing is another reason to hone a cylinder before installing new seals. Deglazing will, in effect, restore the original crosshatch finish that will improve lubrication, minimize wear and offer smoother operation. Honing can also be considered an inspection tool. After a light hone, surface imperfections may be revealed that could indicate a more severe condition.
When to Hone?
Every time a cylinder is resealed, light honing should be performed as part of a thorough repair. It is widely accepted that honing when resealing will save you time and money when you consider the costs of more frequent rebuilds, shortened seal life and lost time. A suitable hone job will renew the bore finish and provide a true bore that is necessary to achieve maximum life, peak performance and reduced downtime.
In some instances, cylinder damage is too severe and a light hone will not be sufficient. In such cases, the hydraulic repair experts at Complete Hydraulic Service can offer several options for a sound repair.
DON’T SKIP CRITICAL STEPS WHEN REBUILDING – ALWAYS HONE YOUR CYLINDERS
For more information, call us.
Proper storage of a hydraulic hammer is crucial for receiving the expected life out of your hammer. As tough as a hydraulic hammer is on the outside, the inside components are just as sensitive to the outside elements. To get the life expectancy you need, store your hammer with these two steps in mind:
If your hammer is not stored standing up and resting on the tool tip, the tool can slide down to the extended position. When this happens, the piston on the inside of the hammer can also slide to the extended position and be exposed to the outside elements. The piston is made of hardened steel and will rust when exposed to moisture. Once the piston starts to rust it is no longer usable and must be replaced. The piston is also one of the most costly parts of a hydraulic hammer to replace.
Hammer Maintenance 30-30 rule
Two easy steps to extend the life of your hammer.
Following these two simple steps will ensure a long life with minimal wear.
Our in-depth inspection process includes measuring the pin eyes for proper size, out of round, straightness, and taper. Sometimes the pin eyes are so worn it’s obvious they need repaired, but sometimes it’s not as obvious and requires the attention of a trained technician.
This important step ensures the proper fit of bearings and pins. It also ensures that alignment is correct while preventing damage to welds, cylinder rods, or eye bearings and also protects against unnecessary wear on the ID of the head gland. As a result, our customers benefit from a better long-term value for the repair.
When it comes to O-Rings (and seals in general) there is more than what meets the eye. It’s critical to have the proper size O-Ring to match the proper squeeze in its groove. This deformation is what causes the O-Ring to seal under pressure.
The material type (buna, viton, etc.) and density (durometer) are also critical to pressure and the associated application. It’s always best to use the O-Ring designed for the application due to temperature, groove depths, and pressure requirements.
We can’t stress it enough, with so many metric sizes being similar to SAE sizes, it’s critical to confirm the proper size.
Experts agree that the number one enemy of a hydraulic system is fluid contamination. Consider these statistics as evidence supporting the negative effects of contaminated oil:
For more information, call us.
Simply stated, contamination is the presence of any unwanted substance in the fluid above acceptable levels. Contaminants can be classified into two broad categories: chemical and particle.
Water is the most common chemical contaminant. Some sources of water could be condensation, environment or make-up oil. Particle contaminants are common and comprise a lengthy list; some examples include dirt, cloth fibers and wear particles. Sources of particle contamination are nearly unlimited. A few common sources are make-up oil, replacement components, hoses and fittings, wear particles and the environment.
For more information, call us.
All hydraulic systems are, or will become, contaminated at some point. The level of contamination varies based on applications and environment. Contaminants come to exist in a hydraulic system in one of three ways:
Contamination Control Practices
Hydraulic systems will always have some level of contaminants present. Listed below are four fundamental concepts that every system owner should consider for a comprehensive contamination control program.
Exclusion – Excluding contaminants from ever entering a system
Removal – Removing contaminants before the system is damaged
Measurement – Measure system contamination at regular intervals
Improvement – Monitor results and continuously seek improvements
For more information, call us.
Complete Hydraulic Service offers a Complete Fluid Analysis (COA) service using our own in-house Fluid Analysis Lab. Our skilled technicians will report results that can provide valuable information to be used for establishing a contamination benchmark. The COA program is also a critical tool for ongoing management and continuous improvement of hydraulic systems. Complete Hydraulic Service is here to help you develop an effective contamination control program and start living a contamination control lifestyle.
For more information, call us.
Oil sample analysis measures wear metals and dirt, detects water, fuel and antifreeze in oil, measures soot, oxidation and sulfur contaminants. Many companies evaluate oil composition, but interpreting the results is the key to effective engine management. We understand your engine, so we can interpret findings and diagnose problems quickly and accurately. Sample at consistent intervals to detect potential problems early.
Engine Coolant Sampling – Over 40% of all engine failures can be traced to the cooling system. Ohio CAT’s Fluids Analysis Lab’s coolant analysis program monitors glycol, supplemental coolant additives, pH levels, conductivity, metal corrosion and other impurities.
Fuel Sampling – If your fuel is being stored for more than a year, there’s a 50% chance that it’s contaminated with water and/or algae, posing a serious threat to the dependable operation of your system. Our fuel sampling program provides a cost effective way to routinely check for contaminants and ensure your engine operates when needed.
Overview of S-O-S Oil Reports
S-O-S Services are valuable management tools that can maximize your equipment life and productivity. At the same time operating costs and downtime can be reduced. During oil analysis, four types of tests are performed on engine, hydraulic and drivetrain oils:
For more information, call us.
Chrome plating, also known as hard chrome, is a technique of electroplating that applies a thin layer of chromium onto a metal object. Chrome plating is used to provide a working surface that requires one or more of the following characteristics: to reduce friction, resist abrasion, or increase corrosion resistance. It is very hard, measuring between 66 to 70 HRC. Surface defects and roughness are amplified because hard chrome does not have a leveling effect.
Friction between a cylinder rod and its seals, and the resulting wear, has a crucial influence on the efficiency and service life of a hydraulic cylinder. Chrome plating is a cost-effective repair option that can allow salvage of a cylinder rod, cylinder tube, or valve spool instead of replacing it with new.
In addition to the cost benefits, chrome plating also creates a hardened wear surface, extending the life of most high wear areas resulting in longer run times between repair or replacement of shaft seals. It can also be used to build thickness on bearing journal areas as well as, valve spools to ensure proper fit when the housing needs to be honed to remove scoring.
Chrome plating is recommended in cases where existing chrome is damaged, worn through to the base metal, scored or dented. Cylinder rod damage can allow contaminants to enter the hydraulic system which accelerates seal wear and eventually cause internal leaks. Chrome plating restores the cylinder rod surface to like-new condition or in some cases better than OEM specifications.
After the chrome is stripped from the damaged part, repairs, if needed to base metal, can be made to include welding and grinding of any imperfections. After any necessary repairs are made, the part then goes through the extensive chrome plating process.
In tough work conditions, the cylinder rods are usually exposed to extreme environments. Consequently, a high quality, protecting layer of chrome on rods with good toughness, corrosion protection and wear resistance is crucial for hydraulic cylinder performance.
There are many types of cylinder rod materials used today. They are measured by several factors including hardness of the surface, yield strength, rod coatings, and composition.
We strive for excellence and use induction-hardened 100YIH chrome-plated material as our standard. This material has a harder surface for abrasion resistance as well as a composition that has the highest standard yield strength in the industry. It gives our customers the best cylinder rod for years of trouble-free service in the most abusive environments.
Rechroming cylinder rods is a standard practice in the industry. It’s required when a cylinder rod has scoring that can’t be polished out with a machine polish. This process removes the existing chrome, straightens the rod, and then applies a new layer of hard chrome. Finally, it gets polished to standards for surface preparation. Rechroming is more cost effective than purchasing new or machining a new rod.
A new rod should be machined if the wear is extended into the base metal, the rod is bent significantly, or the rod is cracked. We carry the materials necessary to make a new rod as well as replacements for broken or heavily damaged parts, which speeds up the process. Machining is more expensive than rechroming but often less than OCM parts, making it a value for our customers.
It’s critical to disassemble and inspect a pump before testing the components. This ensures an efficient testing process, while also saving customers’ valuable time and money.
Without thoroughly inspecting the component first, there’s a high risk a failed component could be going onto the test bench, creating an unsafe situation for our technicians. This also increases the risk of damaging the test bench by introducing contamination. If the test bench becomes damaged, it would delay or stop our testing capabilities for all our customers. Oftentimes, we learn just as much or more disassembling the component as we would testing it.